CASESTUDY กรณีศึกษา
Geomagic Control Xการออกแบบอุตสาหกรรมและการผลิต
การวัดรูปร่างด้วยการสแกน 3D ช่วยเพิ่มความคล่องตัวในกระบวนการตรวจสอบ!
เข้าสู่วงการวิศวกรรมย้อนกลับ
Asano Co., Ltd.
2021.07.15 อัปเดต
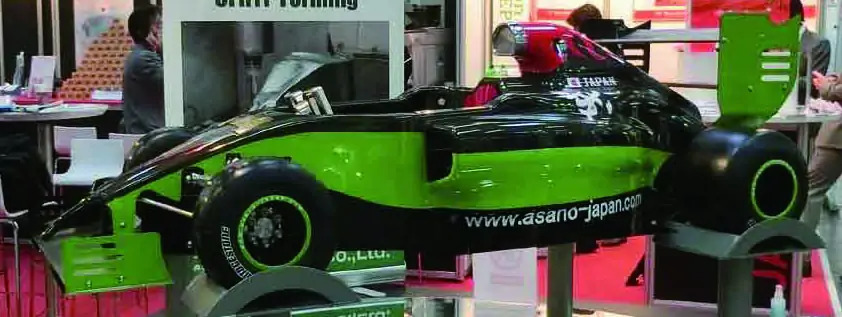
เทคโนโลยีการวัดรูปร่างที่เร่งการตรวจสอบได้ 2-3 เท่า
Asano Co., Ltd. เป็นผู้ผลิตการแปรรูปโลหะที่ให้การสนับสนุนการพัฒนาและบริการสนับสนุนการเตรียมการผลิตสำหรับผู้ผลิตรถยนต์และรถจักรยานยนต์ พัฒนาการผลิตและพัฒนาชิ้นส่วนโลหะแผ่นต้นแบบ, แม่พิมพ์อัดสำหรับการผลิตจำนวนมาก, แม่พิมพ์ฉีดเรซิน ฯลฯ เป็นที่รู้จักจากฐานเทคโนโลยีขั้นสูงที่หลากหลายและแนวทางเชิงรุกเพื่อใช้เทคโนโลยีที่ทันสมัย
คุณ Kishi ผู้จัดการสำนักงานส่งเสริมการจัดการ กล่าวว่า:
“ตัวอย่างเช่น เพื่อตอบสนองความต้องการที่เพิ่มขึ้นอย่างรวดเร็วในการลดน้ำหนักในอุตสาหกรรมยานยนต์ เรากำลังดำเนินการพัฒนาร่วมกันโดยใช้ CFRTP (เทอร์โมพลาสติกเสริมแรงด้วยคาร์บอนไฟเบอร์) คาดการณ์ความต้องการและรับมือกับความท้าทายก่อน นี่เป็นหนึ่งในจุดแข็งของเรา” วัฒนธรรมที่ท้าทายนี้พบเห็นได้ทั่วไปไม่เฉพาะในแผนกการผลิตแต่ละแผนกเท่านั้น แต่ยังรวมถึงในแผนกประกันคุณภาพของบริษัทด้วย
คุณ Imai ผู้จัดการแผนกประกันคุณภาพโรงงานกุนมะ กล่าวว่า:
“ที่แผนกประกันคุณภาพของโรงงานกุนมะซึ่งส่วนใหญ่ผลิตชิ้นส่วนโลหะแผ่นต้นแบบ ความท้าทายคือวิธีลดจำนวนการทดลองและวิธีรับแม่พิมพ์ในช็อตเดียว ด้วยเหตุนี้ เราจึงแนะนำและใช้ประโยชน์จากสิ่งใหม่ ๆ เทคโนโลยี เรายังส่งเสริมสิ่งนี้อย่างแข็งขัน” หนึ่งในความพยายามของแผนกประกันคุณภาพคือการจัดตั้งวิธีการตรวจสอบแบบใหม่ที่รวดเร็วและแม่นยำยิ่งขึ้นเพื่อแทนที่การตรวจสอบแบบเดิม เบื้องหลังนี้คือปัญหาของการวัดรูปร่าง ซึ่งเป็นปัญหาสำหรับการตรวจสอบต้นแบบมาหลายปีแล้ว
“สิ่งสำคัญคือต้องเข้าใจรูปร่างและพื้นผิวโดยรวมเมื่อสร้างต้นแบบ แต่ก่อนหน้านั้นไม่มีวิธีใดเลย เราไม่มีวิธีการวัด ดังนั้นเราจึงไม่สามารถเข้าใจปริมาณความเบี่ยงเบนที่แท้จริงได้อย่างง่ายดาย” มัตสึโมโตะ ผู้รับผิดชอบการตรวจสอบแผนกประกันคุณภาพกล่าว ในขณะนั้น ที่สถานที่ผลิตต้นแบบ มีการพิจารณาวิธีการหลายวิธีเพื่อค้นหาวิธีการจับค่าความเบี่ยงเบนที่แท้จริงเป็นค่าตัวเลขเฉพาะ และสิ่งที่พบก็คือการวัดรูปร่างด้วยอุปกรณ์วัดสามมิติแบบแขนกล
“เราเปิดตัวเครื่องมือวัด 3D แบบมีแขนกลนี้ในปี 2004 โดยเป็นเครื่องแรกในอุตสาหกรรม ขณะเดียวกัน เราได้เปิดตัว Geomagic Control ซึ่งเป็นซอฟต์แวร์ตรวจสอบรูปร่างที่มีประวัติการทำงานที่พิสูจน์แล้วเมื่อใช้ร่วมกับอุปกรณ์นี้ ซึ่งนำไปสู่การสร้างวิธีการวัดรูปร่างแบบใหม่” (คุณมัตสึโมโตะ)
Geomagic Control เป็นแพลตฟอร์มการตรวจสอบอัตโนมัติที่ปรับปรุงกระบวนการตรวจสอบในสายการผลิตและแบบซ้ำ ๆ โดยใช้เครื่องสแกน 3D และเครื่องวัดพิกัดแบบแขนกล รองรับเครื่องมือวัดแบบสัมผัสและแบบไม่สัมผัสที่หลากหลายและเพิ่มประสิทธิภาพสูงสุด ด้วยการใช้ Geomagic Control ร่วมกับเครื่องมือวัด 3D แบบแขนจับ การตรวจสอบต้นแบบที่รวดเร็วและแม่นยำยิ่งขึ้นจึงเกิดขึ้น
“ในอดีต เมื่อต้นแบบถูกกดและวัดด้วยเลเซอร์และผลที่ได้คือ NG เป็นการยากที่จะระบุได้ว่าเป็นปัญหาที่รูปร่างหรือปัญหาของเลเซอร์หรือไม่ และใช้เวลานานมาก โดยการทำเช่นนี้ทำให้เราสามารถเข้าใจสาเหตุได้อย่างรวดเร็ว เราสามารถเร่งการตรวจสอบได้ 2 ถึง 3 เท่า ซึ่งช่วยปรับปรุงประสิทธิภาพได้อย่างมาก” (คุณมัตสึโมโตะ)
ขจัดการทำงานด้วยตนเองที่ไม่จำเป็นและทำให้งานการวัดคล่องตัว
การควบคุม Geomagic และการวัดรูปร่างโดยเครื่องมือวัด 3D แบบแขนกลที่นำมาใช้ในลักษณะนี้ ได้ขยายช่วงการใช้งานและเปลี่ยนวิธีการตรวจสอบไปพร้อมกับการปรับปรุงประสิทธิภาพของ PC
“เราใช้เครื่องวัด 3D การตรวจสอบอุปกรณ์จับยึด และเครื่องมือจับยึดเพื่อตรวจสอบคุณลักษณะของผลิตภัณฑ์ แต่นั่นเป็นเพียงผลิตภัณฑ์ที่ผลิตเป็นจำนวนมากเท่านั้น และอุปกรณ์ตรวจสอบอื่น ๆ ไม่สามารถทำได้เนื่องจากปัญหาด้านต้นทุนและเวลา” (คุณมัตสึโมโตะ)
ดังนั้น ยกเว้นผลิตภัณฑ์ที่ผลิตในปริมาณมาก จึงเป็นเรื่องยากที่จะเข้าใจรูปร่างโดยรวม เนื่องจากไม่มีทางเลือกอื่นนอกจากต้องยืนยันตำแหน่งรูด้วยการวัด 3D และวัดพื้นผิวที่จุดใดก็ได้ ในการแก้ไขผลิตภัณฑ์ประเภทเฟรมประเภทเฟรม ตำแหน่งของรูถูกวัดโดยการกำหนดจุดเอง และสถานที่ที่อยู่นอกพิกัดความเผื่อได้รับการแก้ไขด้วยฝีมือช่าง แต่สิ่งนี้ทำให้เกิดจุดเปลี่ยนอีกครั้งและทำให้จับรูปร่างโดยรวมได้ยาก เป็นผลให้ใช้เวลาและความพยายามอย่างมากในการชี้แจงภูมิหลัง
“หลังจากการแนะนำ Control คำสั่งก็กลับกันโดยสิ้นเชิง โฟลว์เริ่มต้นด้วยการสแกนก่อนเพื่อจับรูปร่างโดยรวมและจับเทรนด์ ตอนนี้ เราสามารถตัดสินใจได้อย่างรวดเร็ว” (คุณมัตสึโมโตะ)
หลังจากนั้น เราได้ทำการแก้ไขด้วยมือ สแกนอีกครั้งเพื่อตรวจสอบความผิดเพี้ยน และหลังจากทำขั้นตอนนี้ซ้ำแล้วซ้ำอีก เราได้กำหนดขั้นตอนการตรวจสอบการเปลี่ยนแปลงโดยรวมและทำการวัดให้เสร็จสิ้น
เข้าสู่วงการวิศวกรรมย้อนกลับ
“เราติดตั้ง Geomagic Design X ประมาณปี 2008 เราติดตั้งมันเมื่อเราซื้อเครื่องมือวัดแบบไม่สัมผัสแบบกล้อง อันที่จริง มันไม่ได้ใช้งานมากนัก มันจึงน่าสนใจที่จะใช้มันในเวลาว่างของฉัน” คุณอาเบะ หัวหน้ากลุ่ม CAD Machining General Gr. เขาเป็นผู้เชี่ยวชาญในเครื่องมือดิจิทัลที่ทำการตัดเฉือนโดยใช้ CAD, CAM, CAE เป็นต้น
“ฉันสนใจวิศวกรรมย้อนกลับ ซึ่งเป็นประเด็นร้อนในตอนนั้น และได้ลองทำหลายอย่าง ในที่สุด โปรเจ็กต์ก็ได้เริ่มต้นขึ้นภายในบริษัท และใช้ Design X ที่นั่น”
มันเป็นวิศวกรรมย้อนกลับของตัวรถวิทยุบังคับ การสแกนรูปร่างของตัวรถวิทยุบังคับที่มีอยู่
เราประมวลผลข้อมูลใน Design X สร้างแบบจำลอง solid ตามคุณลักษณะ ตั้งค่าแม่พิมพ์ และสร้างแบบจำลองที่ควบคุมด้วยคลื่นวิทยุที่มีรูปร่างเหมือนกันจากโลหะอัด ความรู้ที่ค่อย ๆ สะสมในลักษณะนี้นำไปสู่การพัฒนาสาขาใหม่ที่เรียกว่าวิศวกรรมย้อนกลับ
“ตั้งแต่นั้นมาเป็นเวลา 5 หรือ 6 ปีแล้ว และเราได้ทำวิศวกรรมย้อนกลับแล้วมากกว่า 200 รายการ โดยเฉพาะอย่างยิ่ง คำสั่งซื้อเพิ่มขึ้นอย่างมากเนื่องจากเราปรับปรุงความแม่นยำของข้อมูลการวัดโดยการรวมเข้ากับอุปกรณ์วัด 3D แบบแขนกล” (นายอาเบะ)
วิศวกรรมย้อนกลับของบริษัทกำลังเติบโตเป็นเสาหลักของธุรกิจใหม่
―― โครงการที่เป็นสัญลักษณ์ของการพัฒนาผลิตภัณฑ์ใหม่ตามคำเรียกร้องของผู้ผลิตเครื่องจูนเนอร์/ชิ้นส่วนรถยนต์ฮอนด้า Spoon Co., Ltd.
นี่คือแผ่นแข็งแบบใหม่ “STIFF PLATE FRONT” ที่รวมแขนส่วนล่างด้านซ้ายและขวาของส่วนหน้าของ HONDA “S660” เข้ากับตัวถัง ด้านหน้าของ S660 มีโครงสร้างแบบโมโนค็อกที่ไม่มีซับเฟรม แต่ GUSSET PLATE ของแท้ที่ส่วนติดตั้งแขนส่วนล่างไม่แข็งแรงพอ และการบิดตัวเกิดขึ้นระหว่างการเบรกอย่างหนักและม้วนตัว เพื่อชดเชยสิ่งนี้ เรากำลังพยายามทำการค้าแผ่นแข็งที่รวมแขนส่วนล่างด้านหน้าด้านซ้ายและขวาเข้ากับตัวรถด้วยผลิตภัณฑ์กดแบบเดียวกับชิ้นส่วนของแท้
“เนื่องจากผลิตภัณฑ์เหล่านี้สร้างขึ้นบนพื้นฐานของตัวรถ การพัฒนาจึงใช้เวลานาน ดังนั้นเราจึงทำวิศวกรรมย้อนกลับด้วย Geomagic Control และ Geomagic DesignX”
คุณมัตสึโมโตะที่กล่าวเช่นนั้น ได้รวบรวมข้อมูลที่ด้านล่างของ S660 โดยการสแกนและประมวลผลด้วยการควบคุม จากข้อมูลนี้ คุณอาเบะดำเนินการวิศวกรรมย้อนกลับกับ Design X การสแกน S660 จริงทำให้แปลงเป็นข้อมูลที่แม่นยำได้ และสามารถดำเนินการตรวจสอบหลายแง่มุมได้อย่างรวดเร็ว แผ่นแข็งที่เสร็จสิ้นด้วยวิธีนี้ติดตั้งง่ายโดยไม่ต้องใช้เครื่องจักร และมีความแม่นยำในการติดตั้งฝาครอบใต้หลังคาได้ดังเดิม และด้วยการรวมระบบกันสะเทือนและตัวถังไว้ในกล่องเดียวเหมือนเฟรมย่อย ทำให้สามารถเคลื่อนที่ได้อย่างมั่นคง
“วิศวกรรมย้อนกลับยังคงมีศักยภาพที่ดี ในช่วงไม่กี่ปีที่ผ่านมา มีการเปิดตัวซอฟต์แวร์วิศวกรรมย้อนกลับอื่น ๆ แต่ Design X ดีที่สุดเพราะมีความสมดุลที่ดีของฟังก์ชันทั้งหมดและสามารถจัดการกับ point clouds ขนาดใหญ่ได้อย่างง่ายดาย Design X ไม่ได้มีแค่การสร้างแบบจำลองแบบทึบตามคุณสมบัติเท่านั้น แต่ยังรวมถึงวิธีการสร้างแบบจำลองที่หลากหลาย เช่น การสร้างพื้นผิวอัตโนมัติ ดังนั้นฉันจึงใช้ฟังก์ชันที่แตกต่างกันขึ้นอยู่กับวัตถุประสงค์ ยังมีอีกหลายสิ่งที่ฉันอยากลอง ดังนั้นฉันจึงต้องการท้าทายตัวเองอย่างแข็งขัน (นายอาเบะ)